Deck : 9 Process Integration
Question
Question
Question
Question
Question
Unlock Deck
Sign up to unlock the cards in this deck!
Unlock Deck
Unlock Deck
1/5
Play
Full screen (f)
Deck : 9 Process Integration
1
Explain the various strategies for the procurement, fulfillment, and production processes.
Strategies for the procurement processes
Procurement process is elicited by a requirement from processes such as fulfillment, material, and production planning process.
Procurement process follows the following two strategies:
• Procure-to-stock
• Procure-to-order
Procure-to-stock:
The procurement strategy "procure-to-stock" is triggered by fulfillment (trading goods), and production (raw materials) planning process.
Procurement process in the company is executed in-order to complete customer orders and to maintain inventory of materials.
Procure-to-stock strategy uses inventory of materials as a buffer between fulfillment, material, and production planning processes to separate them as individual process or to reduce the dependency between the processes.
Procure-to-order:
The procurement strategy "procure-to-order" is triggered by material planning process.
Procure-to-order strategy does not maintain inventory of materials. Fulfillment triggers the procurement process when this strategy is employed in the company for trading goods.
Again production process triggers procurement process when this strategy is employed in the company for raw materials.
Strategies for fulfillment:
Fulfillment is triggered by an order from customer and it uses different process to complete customer order.
Fulfillment process follows the following strategy:
• Sell-from-stock
Sell-from-stock:
This strategy is used to process availability check procedure to determine material availability based on current inventory and planned receipts from either production process or procurement process.
Sell-from-stock strategy uses inventory of materials as a buffer between fulfillment, procurement, and production planning processes to separate them as individual process or to reduce dependency between the processes.
Strategies for production processes:
Production process is triggered by process involved in procurement proposals which make or buy needed materials to finish customer order.
Production process follows the two fundamental strategies:
• Make-to-stock
• Make-to-order
Make-to-stock (MTS):
In this strategy, customer orders are filled using existing inventory containing finished goods. The companies which employ MTS strategy usually produce large quantity of similar products.
The time required to complete customer orders are reduced by implementing this strategy in company, because the company produce identical products in large volume hence, the customers need not to wait for long time to get their products delivered.
This strategy allows companies to produce in large volume at constant rate, regardless of the demand from customer end.
The simplest make-to-stock strategy in SAP ERP system is "net requirement planning (STRATEGY 10)".
• In the strategy, the system uses calculated PIRs (Planned Independent Requirements) to generate procurement proposals, regardless of CIRs (Customer Independent Requirements).
Variation of MTS strategy:
In SAP ERP system a variation of MTS strategy is referred as planning with final assembly (STRATEGY 40). Like MTS strategy, this strategy is also based on PIRs (Planned Independent Requirements).
• But, unlike MTS strategy, actual sales orders are taken into account in this strategy using a procedure called as consumption.
Make-to-order (MTO):
In this strategy, sales orders trigger the finished goods production and required semi-finished are employed. Inventory for the materials produced in the company are not maintained.
Sales - order - based - production is another name of MTO. The companies which employ MTO strategy usually produce unique products.
Example of MTO is, if a company introduces high-speed cars for racing, it will use MTO strategy to produce these cars. These cars will be produced only after receiving orders from a customer.
Variation of MTO strategy:
Assemble-to-order (ATO) is the variation of MTO strategy, in this strategy inventory of semi-finished goods are required to produce finished goods which is procured to stock. Sales orders trigger the finished goods production just like MTO strategy.
• ATO strategy is utilized in a situation in which there are an extensive number of conceivable designs of end items.
• An example of ATO strategy is, to make a computer different configurations of semi-finished goods can be gathered and put together as a computer.
• The components for finished product are already in stock; hence, generating sales order is an easy process.
• ATO strategy in SAP ERP system is referred as planning without final assembly or subassembly planning (STRATEGY 50).
• Variations of both MTS and MTO strategies give more flexibility in meeting customer requirements.
Procurement process is elicited by a requirement from processes such as fulfillment, material, and production planning process.
Procurement process follows the following two strategies:
• Procure-to-stock
• Procure-to-order
Procure-to-stock:
The procurement strategy "procure-to-stock" is triggered by fulfillment (trading goods), and production (raw materials) planning process.
Procurement process in the company is executed in-order to complete customer orders and to maintain inventory of materials.
Procure-to-stock strategy uses inventory of materials as a buffer between fulfillment, material, and production planning processes to separate them as individual process or to reduce the dependency between the processes.
Procure-to-order:
The procurement strategy "procure-to-order" is triggered by material planning process.
Procure-to-order strategy does not maintain inventory of materials. Fulfillment triggers the procurement process when this strategy is employed in the company for trading goods.
Again production process triggers procurement process when this strategy is employed in the company for raw materials.
Strategies for fulfillment:
Fulfillment is triggered by an order from customer and it uses different process to complete customer order.
Fulfillment process follows the following strategy:
• Sell-from-stock
Sell-from-stock:
This strategy is used to process availability check procedure to determine material availability based on current inventory and planned receipts from either production process or procurement process.
Sell-from-stock strategy uses inventory of materials as a buffer between fulfillment, procurement, and production planning processes to separate them as individual process or to reduce dependency between the processes.
Strategies for production processes:
Production process is triggered by process involved in procurement proposals which make or buy needed materials to finish customer order.
Production process follows the two fundamental strategies:
• Make-to-stock
• Make-to-order
Make-to-stock (MTS):
In this strategy, customer orders are filled using existing inventory containing finished goods. The companies which employ MTS strategy usually produce large quantity of similar products.
The time required to complete customer orders are reduced by implementing this strategy in company, because the company produce identical products in large volume hence, the customers need not to wait for long time to get their products delivered.
This strategy allows companies to produce in large volume at constant rate, regardless of the demand from customer end.
The simplest make-to-stock strategy in SAP ERP system is "net requirement planning (STRATEGY 10)".
• In the strategy, the system uses calculated PIRs (Planned Independent Requirements) to generate procurement proposals, regardless of CIRs (Customer Independent Requirements).
Variation of MTS strategy:
In SAP ERP system a variation of MTS strategy is referred as planning with final assembly (STRATEGY 40). Like MTS strategy, this strategy is also based on PIRs (Planned Independent Requirements).
• But, unlike MTS strategy, actual sales orders are taken into account in this strategy using a procedure called as consumption.
Make-to-order (MTO):
In this strategy, sales orders trigger the finished goods production and required semi-finished are employed. Inventory for the materials produced in the company are not maintained.
Sales - order - based - production is another name of MTO. The companies which employ MTO strategy usually produce unique products.
Example of MTO is, if a company introduces high-speed cars for racing, it will use MTO strategy to produce these cars. These cars will be produced only after receiving orders from a customer.
Variation of MTO strategy:
Assemble-to-order (ATO) is the variation of MTO strategy, in this strategy inventory of semi-finished goods are required to produce finished goods which is procured to stock. Sales orders trigger the finished goods production just like MTO strategy.
• ATO strategy is utilized in a situation in which there are an extensive number of conceivable designs of end items.
• An example of ATO strategy is, to make a computer different configurations of semi-finished goods can be gathered and put together as a computer.
• The components for finished product are already in stock; hence, generating sales order is an easy process.
• ATO strategy in SAP ERP system is referred as planning without final assembly or subassembly planning (STRATEGY 50).
• Variations of both MTS and MTO strategies give more flexibility in meeting customer requirements.
2
Explain the role of inventory in reducing the interdependence among processes.
Interdependence among processes:
The interdependence among processes refers each process in an organization is depends on the other process.
An organization contains six processes; they are,
• "Financial accounting"
• "Procurement"
• "Fulfillment"
• "Production"
• "Inventory and warehouse management"
• "Material planning"
The steps in one process predictably affect the result of other processes.
Role of inventory:
The role of inventory in reducing the interdependence between processes is as follows:
To maintain a stock or inventory of materials in an organization, the production and procurement process has been executed. The stock or inventory of materials is used to fill the customer orders.
If the organization maintains the inventory at proper stock levels, then it not required to start the production or procurement process. Here, the processes in the organization are less dependent to each other.
On the other hand, if the organization does not maintain inventory among processes, then the process of filling customer order must need to execute the procurement or production process to make these processes highly dependent on each other.
The interdependence among processes refers each process in an organization is depends on the other process.
An organization contains six processes; they are,
• "Financial accounting"
• "Procurement"
• "Fulfillment"
• "Production"
• "Inventory and warehouse management"
• "Material planning"
The steps in one process predictably affect the result of other processes.
Role of inventory:
The role of inventory in reducing the interdependence between processes is as follows:
To maintain a stock or inventory of materials in an organization, the production and procurement process has been executed. The stock or inventory of materials is used to fill the customer orders.
If the organization maintains the inventory at proper stock levels, then it not required to start the production or procurement process. Here, the processes in the organization are less dependent to each other.
On the other hand, if the organization does not maintain inventory among processes, then the process of filling customer order must need to execute the procurement or production process to make these processes highly dependent on each other.
3
Identify and discuss the steps in the integrated process that include the procurement, fulfi llment, and IWM processes. Analyze the fi nancial and material impacts of the various process steps.
Integrated process steps:
The step includes fulfillment, procurement, production and inventory and IWM (integrated warehouse management) process.
Fulfillment process (initial steps):
Purchase order triggers this process.
• Process sales order: In this step, it prompts to create the order of sales and it is processed. Then availability check is executed.
• Shipping step: The availability check determines whether the required amount of goods is available.
The initial steps are shown in the diagram:
Procurement process (initial steps):
It triggers the production process and initially, there will be not be sufficient materials in the stock.
• The plant request to create the planned order.
• Once the planned order is authorized, then it is converted to purchase order.
The initial steps for procurement are shown in the diagram:
Procurement process (internal procurement):
The internal procurement is triggered from another plant.
• Initially a STO (stock transport order) is created which transfers the materials from one plant to some other plant.
• After creating the requisition, the good issue is executed by the sending plant.
• After receiving the materials, it is valued with the price.
• In general ledger, there is no change for the material cost.
• Next, it calculates the average price for moving materials and that newly calculated price will be either different or same for the both the plants.
o The status sets the "in-transit" for the material being shipped at the receiving plant.
o Next, it records for the goods receipt at the receiving plant.
o The request for the material with single line item is created.
o Finally, the status is changed from "in-transit" to "unrestricted use".
• There are no financial impacts created in in-house procurement.
The internal procurement process is represented in the diagram:
Procurement process- external procurement:
The external process of procurement is triggered by the insufficient raw material.
• Initially it creates the requisition to purchase
• After requisition is created the order for purchasing is issued to vendor
• When the materials are received from the vendor, the receipt of goods for the purchase is obtained from the vendor.
The financial impacts (FI) occurred includes the steps:
• Initially, a document for material is created with single line.
• The general ledger account is reflected in the inventory account
• The inventory account is debited and the goods receipt/invoice receipt account (GR/IR) account is debited which are recorded by the FI document.
• Along with the production order the approximate planned cost is included.
• After obtaining the invoice, it is verified.
• Then, post the debit of GR/IR account and credits the subledger account of the vendor with the amount as in invoice.
• Finally, to make the payment, the bank account is credited.
• Debit the accounts payable reconciliation account and the subledger account of the vendor with the equal amount.
• Perform the material valuation.
The external procurement process is represented in the diagram:
Warehouse management steps related to procurement:
The steps triggered by the goods receipt in the storage area in the receiving plant are as follows.
• The materials are kept temporarily in the storage area and goods receipt is completed.
• Transfer requirement (TR) is created which in turn triggers the warehouse management process.
• Transfer order (TO) be created in response which authorizes to keep the materials in the bin.
• Then it is transferred to precise storage bin and it confirms the transfer order.
• There are no materials and financial document in warehouse management.
Warehouse management process which is related to STO is shown in the diagram:
Fulfillment process-shipping:
If the process of warehouse management is involved then it triggers the fulfillment process.
• In this shipping process, it creates the delivery documents to authorize then it pick, packs and issues the goods.
Warehouse management steps related to fulfillment:
This process is triggered by the delivery documents in the shipping step.
• After creating the delivery document, the transfer order is automatically created which moves the goods from the storage bins to interim shipping storage area.
• Once the movements of goods are completed then the transfer order is confirmed.
• There are no material or FI impacts.
Warehouse management process is shown in the diagram:
Fulfillment process-concluding steps:
Once the materials moved from the storage area to interim shipping storage area, the concluding steps begins
• Send the goods issue. The following documents are created:
o Creation of material document to show the materials removed from inventory.
o Creation of FI document.
o Debit the account from goods sold and deposit the inventory account.
• Generate the customer invoice. Create the financial impact document.
o Post the charge in the sub ledger account of customer where the accounts receivable reconciliation account is posted manually.
o Post the credit in the revenue account.
• Receive the payment from the customer. Create the FI document
o Post the debit in the account.
o Post the credit in customer account where the accounts reconciliation account is posted manually.
Concluding steps is represented in the diagram:
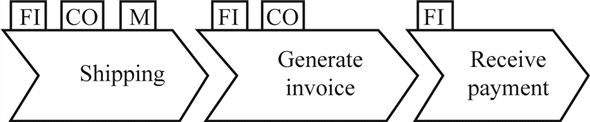
The step includes fulfillment, procurement, production and inventory and IWM (integrated warehouse management) process.
Fulfillment process (initial steps):
Purchase order triggers this process.
• Process sales order: In this step, it prompts to create the order of sales and it is processed. Then availability check is executed.
• Shipping step: The availability check determines whether the required amount of goods is available.
The initial steps are shown in the diagram:
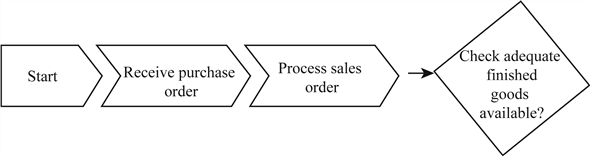
It triggers the production process and initially, there will be not be sufficient materials in the stock.
• The plant request to create the planned order.
• Once the planned order is authorized, then it is converted to purchase order.
The initial steps for procurement are shown in the diagram:
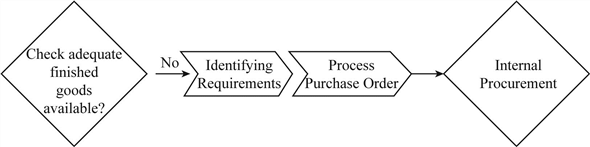
The internal procurement is triggered from another plant.
• Initially a STO (stock transport order) is created which transfers the materials from one plant to some other plant.
• After creating the requisition, the good issue is executed by the sending plant.
• After receiving the materials, it is valued with the price.
• In general ledger, there is no change for the material cost.
• Next, it calculates the average price for moving materials and that newly calculated price will be either different or same for the both the plants.
o The status sets the "in-transit" for the material being shipped at the receiving plant.
o Next, it records for the goods receipt at the receiving plant.
o The request for the material with single line item is created.
o Finally, the status is changed from "in-transit" to "unrestricted use".
• There are no financial impacts created in in-house procurement.
The internal procurement process is represented in the diagram:
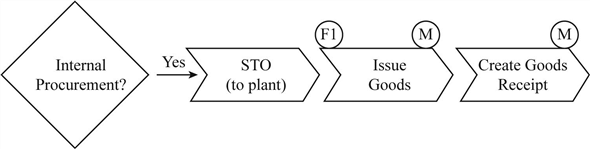
The external process of procurement is triggered by the insufficient raw material.
• Initially it creates the requisition to purchase
• After requisition is created the order for purchasing is issued to vendor
• When the materials are received from the vendor, the receipt of goods for the purchase is obtained from the vendor.
The financial impacts (FI) occurred includes the steps:
• Initially, a document for material is created with single line.
• The general ledger account is reflected in the inventory account
• The inventory account is debited and the goods receipt/invoice receipt account (GR/IR) account is debited which are recorded by the FI document.
• Along with the production order the approximate planned cost is included.
• After obtaining the invoice, it is verified.
• Then, post the debit of GR/IR account and credits the subledger account of the vendor with the amount as in invoice.
• Finally, to make the payment, the bank account is credited.
• Debit the accounts payable reconciliation account and the subledger account of the vendor with the equal amount.
• Perform the material valuation.
The external procurement process is represented in the diagram:

The steps triggered by the goods receipt in the storage area in the receiving plant are as follows.
• The materials are kept temporarily in the storage area and goods receipt is completed.
• Transfer requirement (TR) is created which in turn triggers the warehouse management process.
• Transfer order (TO) be created in response which authorizes to keep the materials in the bin.
• Then it is transferred to precise storage bin and it confirms the transfer order.
• There are no materials and financial document in warehouse management.
Warehouse management process which is related to STO is shown in the diagram:

If the process of warehouse management is involved then it triggers the fulfillment process.
• In this shipping process, it creates the delivery documents to authorize then it pick, packs and issues the goods.
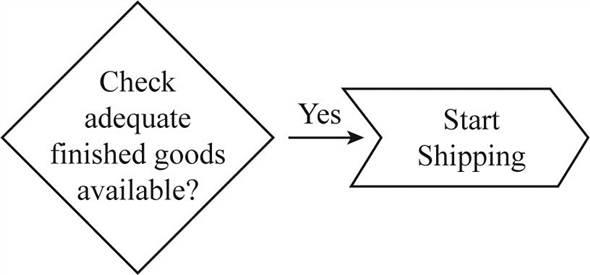
This process is triggered by the delivery documents in the shipping step.
• After creating the delivery document, the transfer order is automatically created which moves the goods from the storage bins to interim shipping storage area.
• Once the movements of goods are completed then the transfer order is confirmed.
• There are no material or FI impacts.
Warehouse management process is shown in the diagram:
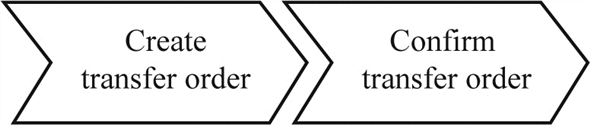
Once the materials moved from the storage area to interim shipping storage area, the concluding steps begins
• Send the goods issue. The following documents are created:
o Creation of material document to show the materials removed from inventory.
o Creation of FI document.
o Debit the account from goods sold and deposit the inventory account.
• Generate the customer invoice. Create the financial impact document.
o Post the charge in the sub ledger account of customer where the accounts receivable reconciliation account is posted manually.
o Post the credit in the revenue account.
• Receive the payment from the customer. Create the FI document
o Post the debit in the account.
o Post the credit in customer account where the accounts reconciliation account is posted manually.
Concluding steps is represented in the diagram:
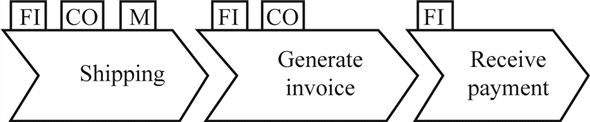
4
Identify and discuss the steps in the integrated process that include the procurement, fulfi llment, production, and IWM processes. Analyze the fi nancial and material impacts of the various process steps.
Unlock Deck
Unlock for access to all 5 flashcards in this deck.
Unlock Deck
k this deck
5
Prepare a process diagram that displays the steps that GBI must execute in order to fi ll a customer order, based on the fi ve assumptions listed below. Make certain to include the fi nancial and material impacts of each step as illustrated in the chapter.
a. Rocky Mountain Bikes has ordered 250 road helmets (RHMT 1000) from GBI.
b. The San Diego plant has 50 road helmets valued at a moving average price of $25.13 each
c. The Miami plant has 400 road helmets valued at a moving average price of $25.25.
d. GBI has decided to move 100 road helmets from Miami to San Diego and purchase 300 helmets from Spy Gear at $25.54 each.
e. GBI sells road helmets for $50 each.
a. Rocky Mountain Bikes has ordered 250 road helmets (RHMT 1000) from GBI.
b. The San Diego plant has 50 road helmets valued at a moving average price of $25.13 each
c. The Miami plant has 400 road helmets valued at a moving average price of $25.25.
d. GBI has decided to move 100 road helmets from Miami to San Diego and purchase 300 helmets from Spy Gear at $25.54 each.
e. GBI sells road helmets for $50 each.
Unlock Deck
Unlock for access to all 5 flashcards in this deck.
Unlock Deck
k this deck